Six sigma green belt and its function in offices
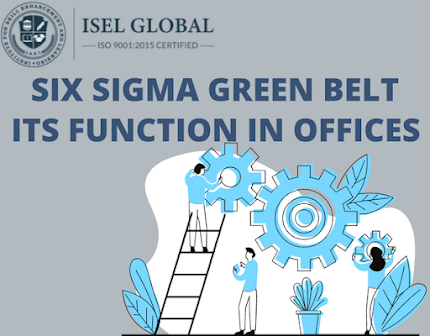
Six Sigma is a set of techniques and tools for process improvement. It was introduced by engineer Bill Smith while working at Motorola in 1986. Six Sigma became popular in the 1990s as a way to improve manufacturing processes. The term "green belt" in Six Sigma refers to the level of training that a person has. Why six sigma green belt As the name suggests, Six Sigma Green Belt is a process improvement methodology that uses data and statistical analysis to identify and eliminate waste, resulting in increased efficiency and productivity. But what does that mean for office workers? Let's take a closer look. In any office environment, there are always opportunities to streamline processes and improve efficiency. That's where Six Sigma Green Belt comes in. This methodology can be used to analyze data and identify areas where improvements can be made. Once these areas have been identified, office workers can then implement changes to help eliminate waste and boost produc...